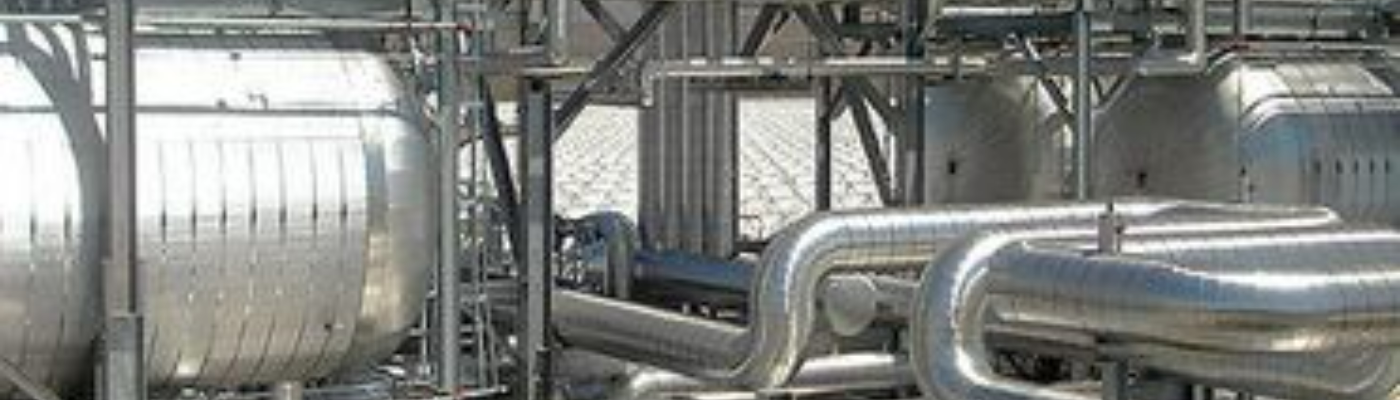
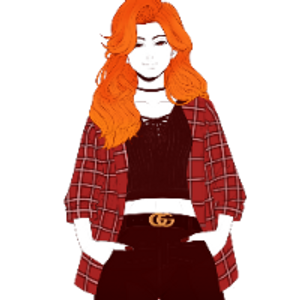
Engineering with Titanium - How to Process Titanium Alloys?
Titanium alloys are difficult to machine using conventional methods. The specific strength of titanium alloy products is very high in metal structural materials. Its strength is equivalent to that of steel, but its weight is only 57% of that of steel. In addition, titanium alloy has the characteristics of small specific gravity, high thermal strength, good thermal stability and corrosion resistance, but it is difficult to cut titanium alloy materials and low machining efficiency. Therefore, how to overcome the difficulty and low efficiency of titanium alloy processing has always been a difficult problem to be solved.
Reasons for difficulties in processing titanium alloys
The thermal conductivity of titanium alloy is small, so the cutting temperature is very high when machining titanium alloy. Under the same conditions, the cutting temperature of TC4 is more than twice that of 45# steel, and the heat generated during machining is difficult to be released through the workpiece; The specific heat of titanium alloy is small and the local temperature rises rapidly during processing. Therefore, the temperature of the tool is very high, the tool tip is rapidly worn, and the service life is reduced.
The low elastic modulus of titanium alloy makes the machined surface easy to rebound, especially the machining rebound of thin-walled parts, which is easy to cause strong friction between the flank and the machined surface, so as to wear the tool and break the edge.
Titanium alloy has strong chemical activity. It is easy to interact with oxygen, hydrogen and nitrogen at high temperature, which increases its strength and decreases its plasticity. The oxygen rich layer formed in the process of heating and forging makes machining difficult.
------------------------------------------------------------------------------------------------------------------------------------------------------------------------------------
Special Titanium Alloys Available Include: Titanium Sheet/Plate Suppliers, Titanium Grade 5 Sheets, Titanium Bars & Rods Suppliers, Titanium Suppliers, Titanium Sheets
-----------------------------------------------------------------------------------------------------------------------------------------------------------------------------------
Cutting principles of titanium alloy materials
In the process of machining, the cutting tool materials, cutting conditions and cutting time will affect the efficiency and economy of titanium alloy cutting.
1. Select reasonable tool materials
According to the properties, processing methods and processing technical conditions of titanium alloy materials, cutting tool materials are reasonably selected. The cutting tool material should be the material with common use, low price, good wear resistance, high thermal hardness and sufficient toughness.
2. Improve cutting conditions
The rigidity of machine tool fixture tool system is better. The clearance of each part of the machine tool should be adjusted well, and the radial runout of the spindle should be small. Fixture clamping work shall be firm and rigid enough. The cutting part of the tool shall be as short as possible, and the thickness of the cutting edge shall be increased as much as possible under the condition of sufficient chip capacity, so as to improve the strength and rigidity of the tool.
3. Properly heat treat the processed materials
The properties and microstructure of titanium alloy materials are changed by heat treatment [III], so as to improve the machinability of materials.
4. Select reasonable cutting parameters
The cutting speed should be low. Because the cutting speed has a great impact on the temperature of the cutting edge, the higher the cutting speed, the sharp increase of the cutting edge temperature. The temperature of the cutting edge directly affects the service life of the tool, so we should choose the appropriate cutting speed.
Machining technology
1. Turning
Turning titanium alloy products is easy to obtain good surface roughness and less severe work hardening, but the cutting temperature is high and the tool wear is fast. In view of these characteristics, the following measures are mainly taken in terms of cutting tools and cutting parameters:
Tool materials: YG6, YG8 and yg10ht are selected according to the existing conditions of the factory.
Tool geometric parameters: appropriate tool front and rear angles and tool tip rounding.
Low cutting speed, moderate feed rate, deep cutting depth and sufficient cooling. When turning the outer circle, the tool tip should not be higher than the center of the workpiece, otherwise it is easy to prick the tool. When finishing turning and turning thin-walled parts, the main deflection angle of the tool should be large, generally 75-90 degrees.
2. Milling
Milling titanium alloy products is more difficult than turning, because milling is intermittent cutting, and the chips are easy to bond with the blade. When the tool teeth of the chips cut into the workpiece again, the chips are knocked off and take away a small piece of tool material to form a broken edge, which greatly reduces the durability of the tool.
Milling method: forward milling is generally adopted.
Tool material: high speed steel M42.
Generally, forward milling is not used for the processing of alloy steel. Due to the influence of the lead screw and nut clearance of the machine tool, during forward milling, the milling cutter acts on the workpiece, and the component force in the feed direction is the same as that in the feed direction, which is easy to cause clearance movement of the workpiece table, resulting in cutting. For down milling, the cutter teeth hit the hard skin at the beginning of cutting, resulting in tool damage. However, because the chip of reverse milling is from thin to thick, the tool is easy to have dry friction with the workpiece at the initial cutting, which aggravates the chip sticking and edge collapse of the tool. In order to mill titanium alloy smoothly, it should also be noted that compared with the general standard milling cutter, the rake angle should be reduced and the rake angle should be increased. The milling speed should be low, and the sharp tooth milling cutter should be used as far as possible to avoid the use of shovel tooth milling cutter.
3. Tapping
For tapping of titanium alloy products, because the chip is small, it is easy to bond with the blade and workpiece, resulting in large machining surface roughness and large torque. Improper selection and operation of tap during tapping can easily lead to work hardening, low machining efficiency and tap breaking from time to time.
The number of standard taps shall be 2-3, and the number of standard taps shall be preferred. The cutting cone angle should be large, and the taper part is generally 3-4 thread length. In order to facilitate chip removal, negative inclination can also be ground in the cutting cone. Try to use short tap to increase the rigidity of tap. The inverted part of the tap shall be appropriately larger than the standard one to reduce the friction between the tap and the workpiece.
4. Reaming
When reaming titanium alloy, the tool wear is not serious, and carbide and high-speed steel reamers can be used. When using cemented carbide reamer, the process system stiffness similar to drilling shall be adopted to prevent the reamer from chipping. The main problem of titanium alloy reaming is that the finish of the reaming is not good. The width of the reaming blade must be narrowed with an oilstone to avoid the bonding between the blade and the hole wall, but sufficient strength should be ensured. Generally, the blade width is 0.1-0.15mm.
The transition between the cutting edge and the calibration part shall be a smooth arc, which shall be polished in time after wear, and the arc size of each tooth shall be consistent; If necessary, increase the inverted cone of the calibration part.
5. Drilling
It is difficult to drill titanium alloy. Knife burning and drill breaking often occur in the machining process. This is mainly caused by poor grinding of the bit, untimely chip removal, poor cooling and poor rigidity of the process system. Therefore, in the drilling process of titanium alloy, we must pay attention to reasonable bit grinding, increase the apex angle, reduce the front angle of the outer edge, increase the rear angle of the outer edge, and add the inverted cone to 2-3 times of the standard bit. Return the cutter frequently and remove the chips in time. Pay attention to the shape and color of the chips. In case of feather or color change of chips during drilling, it indicates that the drill bit has been blunt, and the cutting edge shall be changed in time.
The drilling jig shall be fixed on the workbench, the guide cutter surface of the drilling jig shall be close to the machining surface, and the short drill bit shall be used as far as possible. Another noteworthy problem is that when manual feeding is adopted, the drill bit should not advance or retreat in the hole, otherwise the drilling edge rubs the machined surface, resulting in work hardening and dulling the drill bit.
6. Grinding
The common problems in Grinding Titanium alloy parts are the blockage of grinding wheel and the surface burn of parts caused by sticking debris. The reason is that the thermal conductivity of titanium alloy is poor, resulting in high temperature in the grinding area, resulting in bonding, diffusion and strong chemical reaction between titanium alloy and abrasive. Sticking chips and grinding wheel blockage lead to a significant decrease in grinding ratio. As a result of diffusion and chemical reaction, the workpiece is burned on the grinding surface, resulting in the reduction of fatigue strength of parts, which is more obvious when grinding titanium alloy castings.
The measures taken to solve this problem are:
Select appropriate grinding wheel material: green silicon carbide TL. Slightly lower grinding wheel hardness: ZR1.
The cutting of titanium alloy material must be controlled from the aspects of tool material, cutting fluid and machining process parameters in order to improve the comprehensive efficiency of titanium alloy material machining.
Visit Us: https://steelplates.in/ | https://steelbars.in/ | https://themetalsfactory.com/ | https://steeltubes.co.in/ | https://www.metline-pipefittings.in/